Cement Manufacturing
Basic Stages for Cement ManufacturingThe cement industry is considered one of the strategic industries because it is related to construction and reconstruction. Cement is used as a hydraulic binder from the components of mortar or concrete. However, it is a simple industry compared to major industries, and it depends on the availability of raw materials for that.
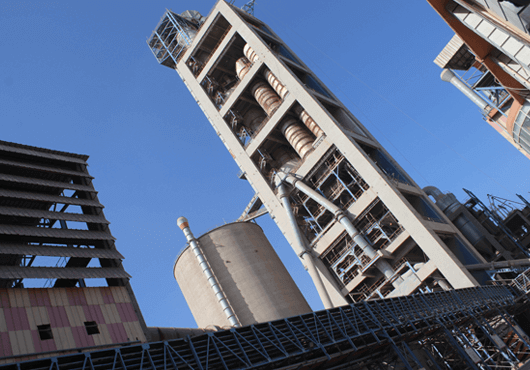

Extraction of Raw Materials :
The raw materials such as limestone and clay needed to produce cement are generally extracted from quarries close to cement plants. Extraction of such materials is done by blasting or the use of special tools and equipment to extract these materials. Before extracting these materials, a pretesting of the percentage of the raw material is conducted at the plant's laboratory to determine the place or location for extraction. After extraction, The raw materials ( being limestone, shale/ clay, iron oxide) are prepared. Gypsum is also made available for cement production.

Firing of Raw Materials :
After grinding and having clean homogeneous raw materials(the rawmix), they are fed into the rotary kiln or furnace that has thermal bricks as lining. The maximum temperature of the firing is 1,450. The basic raw materials to be fired are as follows:
calcium oxide (Cao)
silicon dioxide (Sio2)
aluminum oxide (Al2o3) (Cao)
ferric oxide (Fe2o3); along with some other impurities.

Crushing of Raw Material :
These raw materials are then crushed through a milling process or by Crushers. The size of the crushed raw materials should range between (0-30 mm). The production capacities of crushers differ depending on the need of a cement plant, its production capacity and design.

Blending / Mixing and Storage of Raw Materials :
The raw materials ( limestone + clay) are then transmitted to the first blending storage to be kept in a pyramidal manner in order to be blended thoroughly and properly to produce a fine slurry. A precondition is that the ratio of total carbonate ranges between 76% to 77% and the ration of ferric oxide amounts between 1.2 to 2.5% of the total raw materials to be fed into the raw mill. Ferric oxide ratio depends on its quantity present in the raw materials content (limestone + clay). The process of correctional balancing of the carbonate group by adding pure limestone and clay from the Cementitious storage.

Grinding of Raw Materials :
Following the process of crushing and mixing, the raw materials are then subject to the process of grinding in order to be sintered or fired. This is so the interaction process is done in the least possible time. The production capacities of raw materials mills differ depending on the need of a cement plant, its production capacity and design. There are two common types of mills used; one is ( horizontal ) ball mill and vertical roller mill.

Grinding the Clinker :
the reaction of these raw materials as a result of the sintering, the rawmix is transformed into a substance called clinker. A clinker is chemically composed of Tri-calcium silicate (C3S); Di-calcium silicate (C2S); Tri-calcium aluminate ( C3A); and Tetra-calcium aluminoferrite (C4AF).
(the firing process output) and Adding gypsum: At this stage, the clinker along with the raw gypsum (i.e. calcium sulfate) is finely ground to form the finished cement powder. The fineness of the cement powder should not be less than 2250 mm2 / gram in order to produce fine cement products .

Cement Packaging :
Cement products are packaged in bags whose quality and specifications conform to standard specifications. The capacity of one bag is (50 + -1) kg. Other capacities of cement bags could be offered depending on mutual agreement between the purchaser and seller. Cement could also be given as bulk powder to be blown or pumped into tanks to be loaded on special trucks or vehicles for such a purpose.